Aker Solutions opens new 3D printing center
February 26, 2025
“At Aker Solutions, continuous improvement is at the core of everything we do. That means always looking for ways to enhance efficiency and streamline operations. 3D printing has the potential to revolutionize offshore maintenance, making processes quicker, more cost-effective, and more sustainable. Simply put, if a process can be simplified, we must simplify it,” said Paal Eikeseth, Executive Vice President and Head of Aker Solutions’ Life Cycle segment.
Tuesday of this week marked the official opening of the ADDMO center in Trondheim, held in collaboration with our customer, Equinor. The center was opened as part of a seven-month pilot contract for Equinor’s Troll and Heidrun fields to turn AM ambitions to action within Aker Solutions' maintenance and modification contract.
This is a comprehensive transformation pilot that integrates new workflows, software solutions, and a network of 3D printing facilities. Aker Solutions' management and engineering expertise play a central role from the initial problem-solving phase to the final offshore installation.
The pilot has the potential to be extended, opening new opportunities for offshore asset management innovation.
The benefits of additive manufacturing:
- Reducing emissions: Traditional manufacturing processes generate significant waste, whereas AM enables precise, on-demand production, which in turn means less transport and material use.
- Saving time: When spare parts are unavailable, entire equipment packages may need to be replaced. AM allows for on-demand manufacturing of missing components, reducing downtime.
- Cutting costs: Spare parts are often no longer available in the market due to obsolescence, leading to unnecessary replacement of large equipment packages or systems. Repairing instead of replacing parts helps customers save costs while ensuring operational efficiency.
The center will serve as an innovation hub where engineers working on projects are testing and exploring AM technology, also known as 3D printing, as part of their daily work.
“Working with AM means designing smaller parts of larger equipment, which presents unique challenges for our engineers. We will establish new repair methods, and our ambition is to revolutionize how spare parts are managed under the frame agreement. Exploring and adopting new technologies is key to our digital strategy, and this is a perfect example of how we integrate innovation into our daily work,” said Eikeseth.
Aker Solutions' journey into AM began with another Equinor project, Johan Castberg, where more than 7,000 parts—60% plastic and 40% steel—were successfully 3D printed. This pioneering work laid the foundation for what is now known as “The Castberg Model”, which has evolved into a new 3D-printing lab at Stord, opened in October 2024.
Today, Aker Solutions has over 50 3D printers across its locations and yards, using 3D printing as a tool in various manufacturing processes.
“We must credit Equinor’s ambitions for 3D printing as a driving force behind our journey. Thank you for including us in the learning curve, sharing knowledge, and collaborating to build our digital inventory,” said Aker Solutions’ CEO Kjetel Digre during the opening of ADDMO in Trondheim.
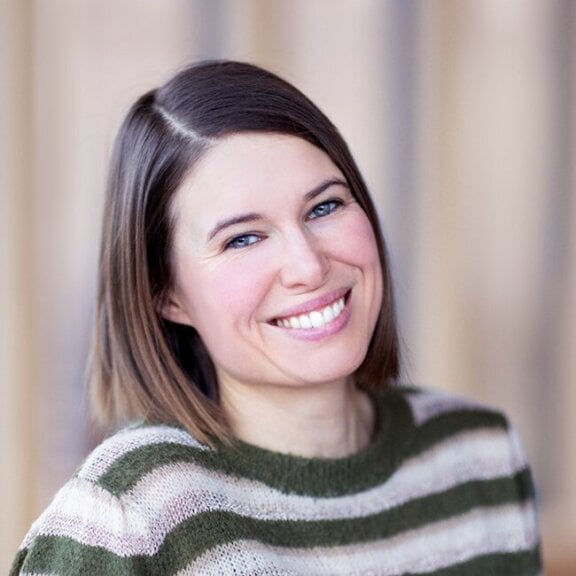